Munition leak testing refers to the process of evaluating the integrity and safety of munition shipping and storage containers to ensure they are free from leaks or any other potential hazards. Leak testing is crucial to prevent accidents, maintain the quality of munition, and ensure the safety of personnel involved in handling and transporting munitions.
Leak Testing Methods
There are several leak testing methods used for munition container leak testing, including visual inspection/water immersion, pressure or vacuum decay, mass flow, and tracer gas testing. Each method has its own advantages and limitations. The choice of method depends on various factors, including the type of munition storage container being leak tested, the desired level of sensitivity and the specific requirements of the end user. It is important to select a method that is appropriate for the specific application and can provide reliable and accurate results.
Visual Inspection/Water Immersion Test
This method involves immersing the munition container in water and applying pressure to simulate real-world conditions. Any leaks or water ingress are detected by visible bubbles during pressurization. Water immersion is the least expensive method. However, this method is time consuming, highly subjective, creates safety concerns and (due to moisture) not suitable for many types of shipping or storage containers or manufacturing environments.
Pressure Or Vacuum Decay Test
Pressure or vacuum decay is used to detect leaks in the 1-1000 sccm leak rate range. For pressure decay, a specific pressure is applied to the container, after stabilizing, the tester measures the decay rate to determine product acceptance. For vacuum testing, a vacuum is created inside the munition container and then monitoring for any increase in pressure over time. If there is an increase in pressure, it indicates the presence of a leak.
During initial setup, the decay characteristics of a “Master” non-leaking container with and without a known leak rate are memorized. Production containers are then referenced to these characteristics to verify the product passes the leak criteria.
Decay testing is simple & inexpensive with good resolution. Large leaks are easy to detect. The smaller the pressure loss being detected, the slower the test. Decay testing is also volume dependent. If the container internal volume varies excessively (part to part) the test results will be variable as well.
Mass Flow Test
Mass flow leak testing is another commonly used method for detecting leaks in the 1 sccm to 200 SLPM leak rate range. Like Pressure Decay, with a Mass Flow the part is pressurized and allowed to stabilize. Once stabile, the leak tester measures the amount of “replacement” air volume needed to maintain the setpoint pressure in the shipping container. Any replacement air required to maintain the setpoint is considered leakage and based on the leak limits applied, the container is passed or rejected.
Mass flow testing is simple & inexpensive with excellent resolution. It is the preferred test method for shipping containers that vary in volume or have large dead volumes. Mass flow has been proven to be less affected by part temperature variation when tested, resulting in less environmental drift.
Tracer Gas Test
Tracer gas testing using helium or hydrogen are the most expensive methods and typically not considered due to its excessive cost and environmental concerns. The method involves introducing a tracer gas into the munition container, then using specialized equipment to detect leakage of the gas. The most used tracer gas for this purpose is helium due to its low concentration in the atmosphere and its ability to penetrate small leaks. A 95/5 Nitrogen/Hydrogen mix is also being used with fair results. Tracer gas testing can provide highly accurate results but requires expertise and is not suitable for most production environments. Significant ancillary equipment will also be required to capture any reusable helium.
In addition to the testing methods mentioned above, there are also international standards and guidelines that provide recommendations for munition container leak testing. These standards include the NATO Standardization Agreement which provides guidelines for the visual inspection and testing of munition containers, and the International Organization for Standardization, which provides guidelines for the leak detection of compressed gas cylinders.
Cutting-Edge Technology
ULTRAFLOW V3
The ULTRAFLOW V3 leak tester is specifically designed to test large internal volume parts such as shipping containers and is configured to test with either pressure decay or mass flow. Occlusion testing is available as well. The UltraFlow utilizes our patented pneumatic design which allows the instrument to test at a faster rate, while eliminating the “false rejects” commonly associated with this type of product.
ULTRAFLOW V3-RT
The ULTRAFLOW V3-RT (Remote Touchscreen) is perfect for smaller workstations with limited space. With this configuration, the HMI can be mounted in a user-friendly location for programming and visual pass/fail status while the instrumentation enclosure can be tucked in a convenient location.
DEFENDER
The DEFENDER tester is considered the best value of any pressure or vacuum decay leak tester on the market. Compact yet powerful, while providing excellent value and return on investment describe the Defender. It’s built for production usage and with Ethernet IP onboard, ready for seamless integration with Allen Bradley devices.
Munition Shipping Container Leak Testing
Why should you leak test munition shipping and storage containers?
Safety
Properly functioning munition and missile systems are crucial for the safety of the world’s military's. Leaks can compromise munition performance, leading to potential accidents. By leak testing companies address this leading in-field safety issue.
Durability
Water or moisture ingress can cause corrosion and munition failures. By identifying and fixing leaks, manufacturers ensure the durability and longevity of the munition they’re protecting.
Regulatory compliance
Munition storage and shipping containers must meet various international standards and guidelines that provide recommendations for munition leak testing. Leak testing helps manufacturers ensure that their products are safe, eliminate moisture ingress, and help address compliance concerns.
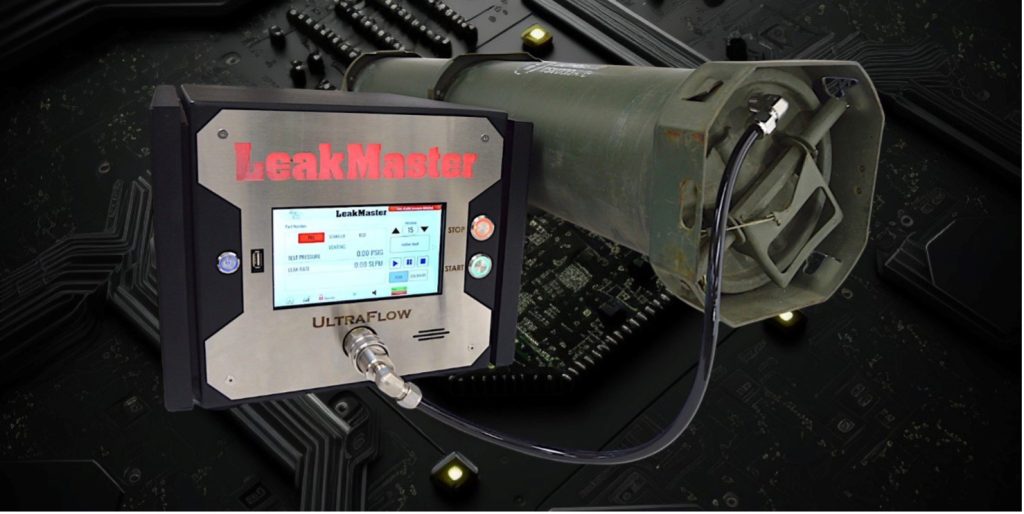
Contact Us Today
Want more information? Contact us for details regarding our leak testers or other products or services.